Our Masterbatches are suited for below applications
Food, non-food and industrial packaging
Coated box board, paper and foil
Extrusion lamination
Fibres for upholstery, carpets, rugs, draperies
Blownware
Injection molded articles
Wires and Cables
Agricultural film: mulch, green house, tunnel
Pipe & conduit
Geosynthetics
Engineering plastic masterbatch
Sanitry ware specialty masterbatch
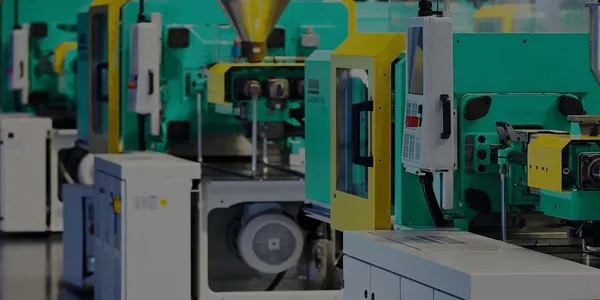
INJECTION MOULDING
The process is used to produce large quantities of identical plastic items. One of the most common types of thermoplastics used in injection molding is high impact polystyrene (HIPS).
Injection Molding is the most important plastics manufacturing process. It produces such small products as bottle tops; sink plugs, children’s toys, containers, model kits, disposable razors and parts of cameras. It is also used to manufacture larger items such as dustbins, and milk crates.
The process can even mould large items such as automotive parts, crates, garden furniture, etc.
BLOW MOULDING
Blow molding commonly uses thermoplastics such as, polyethylene (PE) and polypropylene (PP).
Extrusion blow molding is the most common process for asymmetrical parts which involves the parison in an extrusion process before it is blow molded. The process is for small parts with intricate neck detail.
Multiple parison molding allows multi-layered parts but the process requires close observation as uneven parisons will produce significant waste material.
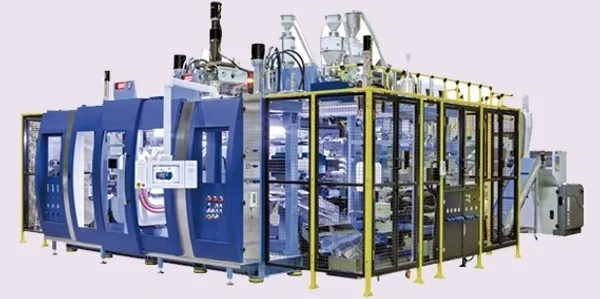
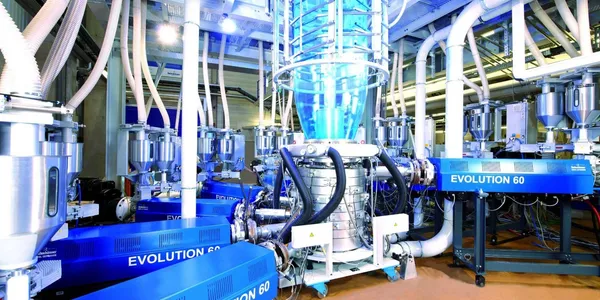
FILM EXTRUSION
Plastic film extrusion is one of the most important processes in plastic industry. It accounts for around a quarter of all thermoplastics consumed and the film extruded is almost entirely for consumption in packaging – particularly food packaging – with the remainder going into agricultural and construction applications.
In its simplest form, the process involves pushing molten polymer through a circular or slot die. This continuous process enables the production of a consistent high quality product to extremely accurate gauge. For most thin gauge films, the film extrusion process takes the form of blown or cast extrusion.
SHEET EXTRUSION
Sheet extrusion is a technique for making flat plastic sheets from a variety of resins. The thinner gauges are thermoformed into packaging applications such as drink cups, deli containers, produce trays, baby wipe containers and margarine tubs. Another market segment uses thick sheet for industrial and recreational applications like truck bed liners, pallets, automotive dunnage, playground equipment and boats. The third primary use for extruded sheet is in geomembranes, where flat sheet is welded into large containment systems for mining applications and municipal waste disposal.
Thermoplastic sheet production is a significant sector of plastics processing. Thermoplastic sheets are flat, plastic materials with a gauge of at least 250 microns and which include both flexible and rigid materials, as well as solid, foamed, and hollow materials.
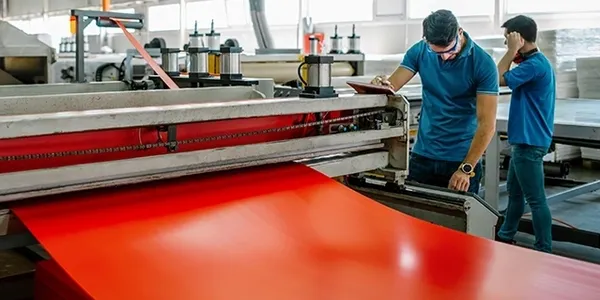
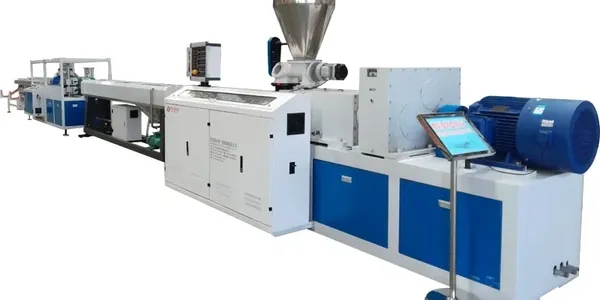
PIPE EXTRUSION
Pipe extrusion is defined as a process of forcing the polymer melt through a shaping die, in this case circular. The extrude from the die is sized, cooled and the formed pipe is pulled to the winder or a cut off device. Prior to this, the plastic material in the form of polymer granules is fed into the hopper, conveyed by a rotating screw through a long cylindrical barrel. This is subjected simultaneously to high temperature and pressure, forcing the melt through the die at a predetermined rate.
ROTOMOULDING
Industrial : Vertical water storage tanks, self-supported horizontal water tank, chemical tanks, pallet bins & pallets, trolleys, septic tanks, ice box, etc.
Agriculture : Water storage tanks, loft tanks, cattle feeders, spray tanks, fuel tanks, grain storage, etc.
Commercial : Buckets, drums, pails, flower pots, road markers, waste bins, toys, swimming pools, sanitary products, etc.
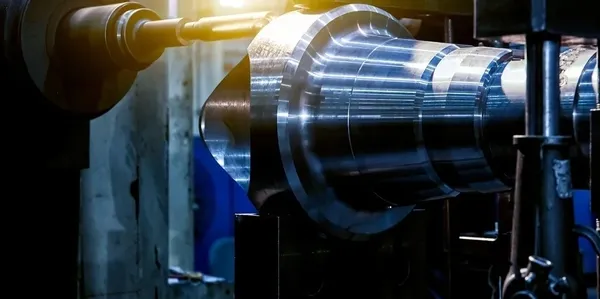
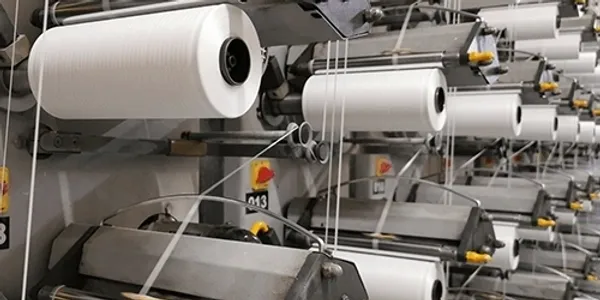
PP AND PE WOVEN SACK EXTRUSION
PP woven sacks
Characterized by excellent compatibility with polyethylene (PE) and polypropylene (PP), Polytec masterbatches can be added to meet the functional requirements of end-use applications, including sacks for cement, chemicals, pet foods, sugars, rice and flour, and block bottom bags.
Benefits of using Polytec propylene-based masterbatch in PP woven sack applications include:
- Outstanding compatibility with PE and PP
- Easy processing
- Down gauging and cost-reduction opportunities
- Low seal-initiation temperature (SIT)
- Controlled surface coefficient of friction (COF)
- Excellent co-extrusion with functionalized tie layer