What is Color Masterbatches
Color masterbatches are concentrated mixtures of pigments and/or dyes that are used to impart color to plastics and other materials during the manufacturing process. They are typically produced in pellet form and can be easily blended with natural or other base resins before processing.
Key points about color masterbatches include:
Composition: They consist of high-quality pigments or dyes combined with a polymer carrier. This helps ensure that the color is evenly distributed throughout the final product.
Convenience: Using masterbatches allows manufacturers to achieve the desired color without the need to handle powders or liquids, simplifying the production process.
Customization: Masterbatches can be tailored to meet specific color requirements, providing flexibility for various applications.
Application: They are widely used in industries such as packaging, automotive, consumer goods, and more, where color consistency and quality are essential.
Cost-Effectiveness: Masterbatches can reduce production costs by minimizing the need for additional coloring agents and improving the efficiency of the coloring process.
Overall, color masterbatches are a crucial component in the production of colored plastic products.
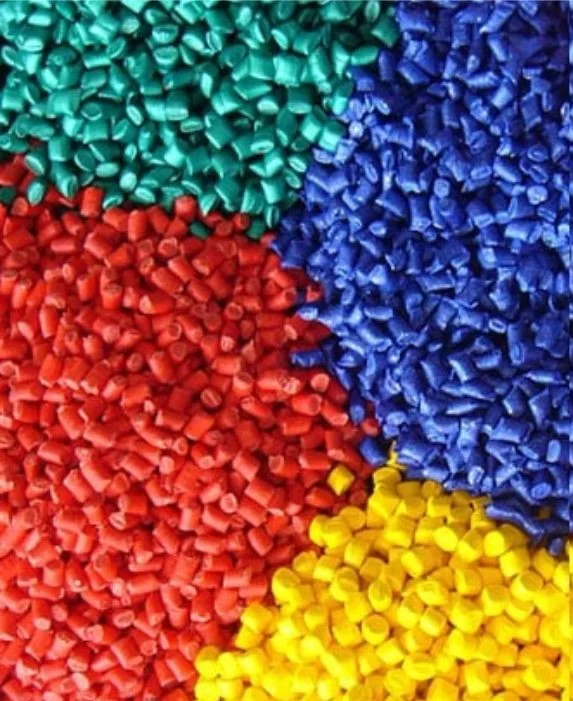
World-class Quality Color Masterbatches
World-class quality color masterbatches are premium formulations designed to deliver exceptional color performance and consistency in a wide range of applications. These masterbatches utilize high-grade pigments and advanced polymer carriers, ensuring superior dispersion and stability throughout the manufacturing process. Rigorous quality control measures and adherence to international standards guarantee that each batch meets the stringent requirements of various industries, from packaging to automotive and consumer goods. With excellent lightfastness, weather resistance, and compatibility with multiple polymers, world-class quality color masterbatches enable manufacturers to achieve vibrant, long-lasting colors while enhancing the overall aesthetic and functional properties of their products. This level of quality not only elevates the visual appeal but also contributes to the durability and market competitiveness of finished goods.
How can you identify the best plastic Color Masterbatch from an average one?
Identifying the best plastic color masterbatch from an average one involves several key factors and testing parameters. Here are some guidelines to help you differentiate between them:
Pigment Quality: High-quality masterbatches use superior pigments that provide better color strength, brightness, and consistency. Look for masterbatches that offer a wide range of color options and excellent color matching capabilities.
Dispersion: A top-notch color masterbatch will have uniformly dispersed pigments, which ensures consistent color throughout the final product. You can assess dispersion quality by checking for any color streaks or inconsistencies in test samples.
Lightfastness and Weather Resistance: The best masterbatches should demonstrate excellent resistance to UV light and environmental conditions, preventing fading over time. Look for performance data or testing results that confirm these properties.
Compatibility: Ensure that the masterbatch is compatible with the base resin you plan to use. High-quality masterbatches are formulated to blend well with various polymers without affecting their physical properties.
Melt Flow Index (MFI): Check the MFI of the masterbatch. A suitable MFI ensures proper processing and flow during manufacturing, contributing to consistent results in the final product.
Physical Properties: Examine the masterbatch for properties like hardness, flexibility, and impact resistance. High-quality masterbatches will not compromise the mechanical properties of the final product.
Supplier Reputation: Consider the manufacturer’s reputation and experience in the industry. Established suppliers often provide better technical support, consistency, and reliability.
Testing and Certification: Look for masterbatches that have been tested and certified by independent laboratories or conform to international quality standards. This can provide additional assurance of their performance and safety.
Cost vs. Value: While price is an important factor, consider the overall value. A slightly higher upfront cost for a superior masterbatch can lead to cost savings in production and improved product quality in the long run.
By evaluating these factors, you can effectively differentiate between high-quality plastic color masterbatches and average ones, ensuring you make informed decisions for your manufacturing needs.
4 traits that are indispensable to high-quality Plastic color masterbatches
Four indispensable traits of high-quality plastic color masterbatches are:
Excellent Color Consistency: High-quality masterbatches maintain uniform color throughout the production process, ensuring that the final products exhibit the same shade and vibrancy without variations. This consistency is crucial for maintaining brand identity and product quality.
Superior Dispersion: A hallmark of high-quality masterbatches is the even distribution of pigments within the carrier resin. This trait ensures that there are no clumps or streaks in the final product, resulting in a smooth and aesthetically pleasing finish.
Durability and Resistance: Quality masterbatches should provide excellent resistance to environmental factors such as UV light, heat, and moisture. This durability ensures that the color remains vibrant and does not fade or degrade over time, extending the lifespan of the final products.
Compatibility with Resins: High-quality color masterbatches are designed to be compatible with various base resins, ensuring seamless blending and processing without negatively impacting the mechanical properties of the final product. This trait allows manufacturers to use the masterbatch across different applications and materials.
These traits are essential for ensuring that plastic products meet performance standards and customer expectations.